When products are destined for outer space it can lead to extensive amounts of aerospace packaging requirements. Manufacturers must keep a strict chain of custody and also comply with rigorous standards to avoid small defects from occurring during shipping and handling. Stakes are high with space exploration because all the equipment needs to work perfectly every time.
The smallest defects can lead to failure to launch. A failure means years of waiting for planetary alignment. The distance between our two planets must be short enough for earth-based equipment to make the journey, any hiccups and all efforts are wasted. The result, is potentially millions of dollars up in smoke.
While this can sound like an intense project, Valley Box thrives on opportunities to contribute to such intricate custom design needs. In this project, we worked to develop a specialized container design to offer 100% contact with the customer's carbon-carbon part while meeting other rigorous aerospace packaging requirements.
Carbon-carbon is a composite material comprised of carbon fiber reinforcement in a matrix of carbon. It has gained a space-worthy reputation due to its high-temperature resistance. It can withstand temperatures from 3,200 to 4,000 degrees Fahrenheit (1760 – 2204°C). The material becomes stronger as it gets hotter!
One-piece Top Box
The customer had an overhead crane at their packing and receiving locations and desired aerospace packaging that would easily allow pick-up by crane. This meant Valley Box designed the top box to be removed in one motion rather than pulling off each panel.
Valley Box designed the top boxwood panels to attach to steel angle rather than traditional wood cleats (which add bulk to box edges for nailing or stapling purposes).
- The 3x3x3/16" steel angle is 20x stronger than 1x4 Doug Fir cleats which built in tremendous strength and integrity
- Internal cleats were not used to provide more interior space and avoid the risk of part contact.
- External cleats would have conflicted with strict outside dimension limitations based on the width of an elevator at the customer's location
Custom Foam Saddle
The customer's part was extremely fragile and it could not be distorted in any way. Inside the box was a custom-shaped saddle constructed of wood + Masonite + foam which provided 100% contact and support to the customer's part. The custom-designed saddle immobilized the part eliminating the risk of distortion which would require re-works or 100% scrapping of the part.
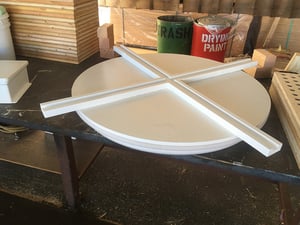
Securing the part on the saddle was a wood X-brace with a circular pad which created even pressure on the customer part so as not to distort it.
Internal tie-down locations had pull-to-tighten straps attached. Ratchet straps were specifically not used to prevent over-tightening and the possible distortion of the part.
Steel Reinforced Design
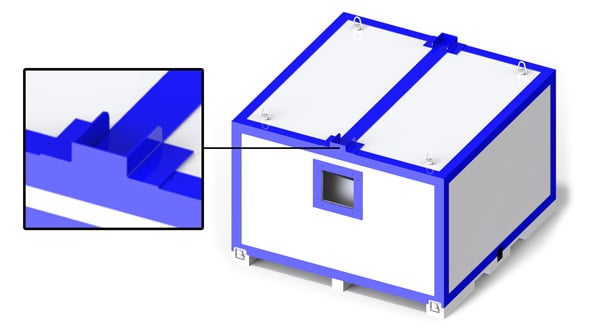
By utilizing steel within the aerospace packaging design we've added strength, reduced weight, and reduced the overall size.
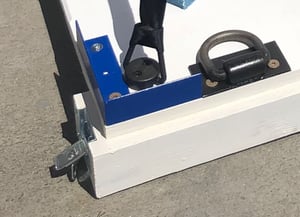
Steel was used in a number of other features such as; inside corner alignments for the top box which allow ease of top box placement.
Steel angle on the exterior of the lid was used for stacking alignment as the customer plans to stack these boxes two high
Observation Viewing Window
Easy access to view important information within your box is extremely important. An observation window was added to the top box so the customer could easily check humidity indicators without needing to open the box as well as eliminating the need to check to see if the box is loaded or unloaded.
Travelers
Typically, paperwork travels with the transportation company and is delivered to receiving personnel. However, often paperwork meant to travel with the shipping crate and its contents become lost or misplaced. With consideration for the immense amount of importance of this part, a waterproof paperwork box was attached to the outside to ensure the customer's paperwork will always travel with the correct part.
Clocking Alignment Marks
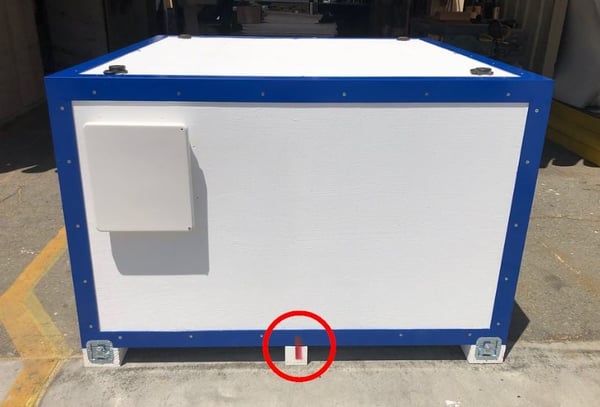
Designing aerospace packaging that is easy to understand and simple to load enables employees' efficiency. Valley Box added featured colored clocking marks and identification numbers to ensure the correct top box gets matched with the correct base and to ensure the lid was going on in the right orientation during assembly.
Fire Retardant
Because bare wood is more susceptible to igniting when next to a heat or flame source, the entire shipping crate, inside and out, was painted with the fire retardant paint. Any products for space and clean rooms cannot have bare wood
To reduce the possibility of coating material being removed when attaching part, all steel components were powder coated. Eliminating the risk of paint chipping off when the unit is mounted to the interface which in turn would then compromise the clean room or the product during transportation.
Forklift access
Valley Box has found its best practice to consider all the people involved with the handling and maneuvering of wood containers. Some people may need to wrestle it into some tight spots, for this reason, we made the crate accessible from all four sides with a 4-way forklift entry.
No matter the industry Valley Box is in the business of creating solutions for even the most complicated of requirements. Designing this nose cone shipping crate is one of many projects we have executed successfully in the aerospace packaging industry and definitely not the last.