OSHA estimates that employers pay almost $1 billion per week for direct workers' compensation costs. These high costs often make companies take a hard look at the costs of workplace accidents which OSHA points out include direct and indirect costs, here are some examples:
Direct costs |
Indirect costs |
Workers' compensation payments Medical expenses Legal services Repairs of damaged equipment and property |
Training replacement employees Accident investigation Implementation of corrective measures Lost productivity Low employee morale Employee absenteeism |
The cost of workplace accidents is a significant problem in just about every industry from manufacturing to food service, so much so that OSHA implemented the “$afety Pays” program, which helps employers assess the impact of occupational injuries on their profitability. $afety Pays is an excellent tool a company can use to determine the costs of workplace accidents, but why not go a few steps further by stopping workplace accidents before they start? One of the most effective ways to do this is to ensure that your workplace utilizes and understands the importance of ergonomic safety equipment.
Ergonomic equipment is designed for specific tasks and environments in such a way as to improve health and safety. Simply put, ergonomics is about fitting the task and equipment to the user. In a manufacturing plant or an assembly line, ergonomic safety equipment is often custom-designed to fit the specific needs of that company. Modern Materials Handling, an online magazine with comprehensive coverage of safety solutions for materials handling professionals, has dozens of articles about companies investing in the improved ergonomics of workers.
Ergonomic Safety Equipment
For an example of a custom design, we turned to a major aeronautics company that needed a material handling and tooling fixture that would "safely and efficiently" 1) remove an airplane tire from the rim, 2) mount the new tire, and 3) seal the bead. Valley Box Company was called for the job. Their engineering team was able to successfully integrate the three steps into just one custom fixture with added safety features to enhance employee ergonomics.
![]() |
![]() |
The result was a "waist-level" fixture that was easily adjusted to accommodate multi-sized tires and included proximity rails to prevent operators from having their hands in a pinch point during operation.
- The tooling fixture decreased safety accidents and increased worker confidence.
- This custom material handling solution helped the company streamline its process, which led to a 30% reduction in labor.
- Valley Box’s custom design also broadened its capabilities because adjusting production lines to accept multiple-sized wheels was no longer an issue.
- The company experienced enhanced productivity with an improved shop throughput time.
- The fixture allowed the company to clear shop floor space and thereby free up more square footage to produce more products and increase output.
Download the entire case study here to learn more.
Material Handling & Tooling Equipment
The different types of material handling and tooling equipment that may be customized to fit your facility or other work environment are plentiful and include, but are not limited to:
- Multi-Use Systems: product build stands, vibration dampening, isolators, staging stands, shipping/handling, and more.
- Positioning Equipment: stock movers, hydraulic post tables, work holding systems, assembly stands, work platforms, stock pickers, and more.
- Storage Equipment: pallet racks, shelving, storage carts, and more.
- Transport Equipment: utility carts, dollies, flat-deck industrial carts, two-tier service carts, mobile storage cabinets, multi-tier stock carts, platform carts, and more.
Valley Box can custom-build ergonomic safety equipment to meet worker mobility requirements. To improve worker ergonomics further, components such as rollers, conveyors, hydraulic lifts, and clamps can be added.
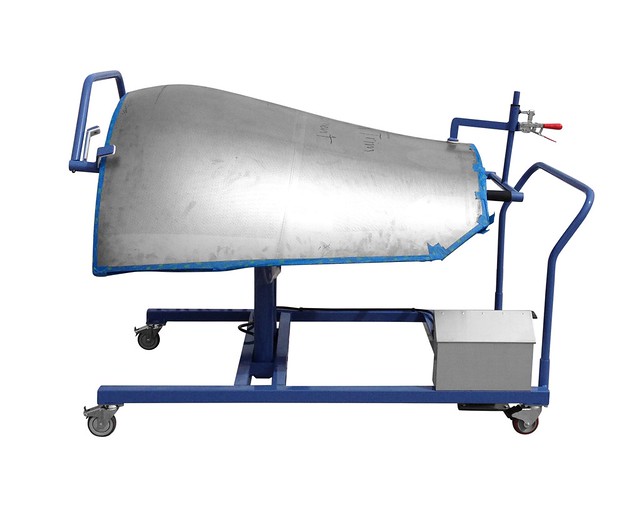