Its the beginning of the year and most likely your company is looking for ways to decrease costs. If you're a manufacturer one of the areas you should be looking at closely is your product's packaging. Here are Valley Box's 6 tips to help you reduce your shipping crate costs this year.
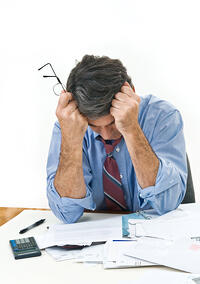
#1 Calculate All Internal Costs
It's good practice to evaluate your internal shipping crate costs. Make sure to factor in all costs such as labor associated with assembly, packing, and handling. Take the time to investigate the challenges your team experiences with the current packaging. Remember, time is money. Need some inspiration? Download this case study below that focuses on Saving Packing Time.
#2 Calculate Damage Costs
Having your products arrive damaged to the end user carries a cost all by itself, there's the cost of return freight, replacement parts and not to mention a dissatisfied customer. If you're experiencing high damage rates then switching to a more robust package may save you money in the long run!
Take the time to let your packaging provider know about both successful and damaged shipments. This will allow them to assess the areas that need improving and the ones that don’t.
To rule out mishandling install damage indicators. If the damage is the result of negligence by the shipping company, they will be responsible for the damages, not you.
Tip: Always supply pictures of packaged products when filing damage claims. This is proof that your shipment was intact when it changed hands.
Watch Valley Box's helpful video about: Preparing for damage claims. ![]() |
# 3 Re-Design
Ask your packaging provider to re-think your shipping crate design with the purpose of reducing costs. This exercise can result in some pretty innovative packaging.
- Maybe you're over packing your product for the amount of time it will be in transit.
- Maybe there are new packaging solutions available that weren't when your original packaging was designed... The times are changing.
- Maybe you need a multi-pack solution because you always ship more than one part.
See how one company saved with a |
Consider how creating Uniform Sizes |
#4 Reusable Packaging
Reusable containers are generally intended to endure long-term use or multiple shipments. This means you can enjoy “re-usability savings” year after year! Sure, purchasing high quality reusable shipping crate may cost more upfront, but opting for a low quality item may inevitably cost you more in the long-term (See #2 Damage Costs). Valley Box offers a variety of sustainable reusable packaging with refurbishing opportunities that will have a positive impact on your pocketbook and the planet.
A reusable shipper |
Reusable boxes can be brought back |
#5 Price vs Service
The price of the packaging isn't the only factor that should be considered. Think about the importance of quality, dependable delivery, and level of customer service. You can do this by rating your own experience first and using only the most reliable sources (online and off) to evaluate other customer experiences. Download Valley Box's helpful guide 10 Questions to Ask Before Hiring a Packaging Company.
#6 Due Diligence
Always getting at least 3 competitive quotes. Quotes are typically quick, easy and free, so if you’re not satisfied with just 3, keep gathering those quotes until you are! Most packaging vendors should have a quote button on their website, and you should expect to hear back within 24 hours.