Reusable shipping crate shipping delays can make a business owner feel helpless and fearful of what may be happening to any sensitive products and materials contained in the shipment.
Even worse is the disappointment customers feel if the shipment doesn't arrive on time. No matter how amazing the product may be, a late shipment can derail customer satisfaction and trust.
In a case study below you'll see how Valley Box was able to make the verification process at customs practically effortless.
I need help with my crate!
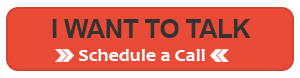
The Challenge
An Equipment Manufacturer was experiencing long wait times at customs because the reusable shipping crate used did not offer easy access for verification.
In addition, during the verification process, the vapor barrier bag was susceptible to being left open exposing sensitive machinery to atmospheric moisture resulting in corrosion damage. The improperly re-sealed containers ultimately led to a 26% damage rate to shipments due to corrosion.
They needed a clever solution that would decrease the time lost and damage caused by overseas customs inspections.
Solution
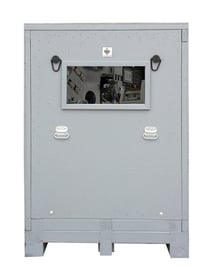
Valley Box installed a viewing window on the exterior of the reusable shipping crate, along with a viewing port in the barrier bag.
This window allowed customs inspectors to perform necessary tasks without breaching the seal or the container.
A humidity indicator visible through the observation port was also added, which provided a method to confirm the integrity of the vapor barrier bag.
Outcome
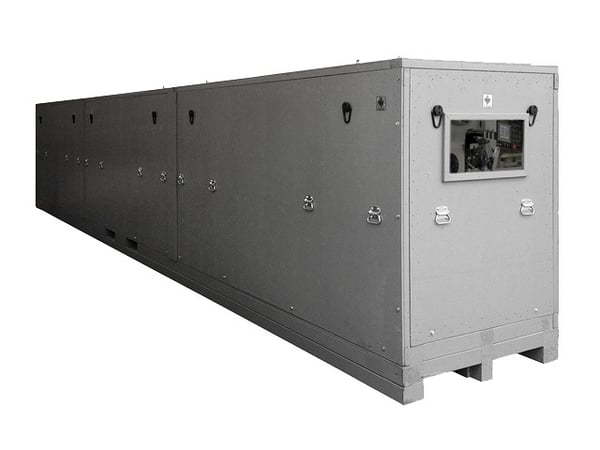
Valley Box’s viewing window on the company’s international reusable shipping crates successfully reduced damage claims to zero and expedited all future customs inspections.
Download Valley Box's case study which explains the design installations used to expedite customs inspections and reduce corrosion damages without a big hit to the bottom line.