Embarking on an exciting mission for the discovery of ancient life NASA's Mars 2020 Rover project is underway! NASA plans to land the rover in Jezero crater, an ancient river delta, which may have proof life once existed on Mars.
"Mars 2020 Sky Crane Processing in PHSF" created by Mars Nasa.gov Credit: NASA / Kim Shiflett |
This huge endeavor requires manufacturing industries to kick into high gear. When these manufacturers ship their parts to the Jet Propulsion Laboratory in Pasadena, CA they can run into a lot of aerospace packaging requirements.
![]() |
"Mars 2020 Media Day" created by Nasa-JPL Copyright: Some Rights Reserved. Hosted on Flickr |
In this project, Valley Box worked to develop two specialized containers for components critical in the journey to Mars. The containers were required to be disassembled for clean room entry, be fire retardant, and meet the rigorous safety requirements.
- The cruise stage phase keeps the spacecraft on course from Earth to Mars with scanners performing system checks, navigation activities, calibrations, and allowing communication. During a cruise, the spacecraft requires periodic spins to maintain the antenna pointing toward Earth and the solar panels pointing to the sun.
- The descent stage provides the power during the entry, descent, and landing phases. It provides guidance, propulsion, and instrumentation to assist with flight. The whole spacecraft has to work perfectly, for virtually the first time, to withstand the 7 minutes of terror that takes the rover from 12,000 mph down to 2 mph! The main job of the descent stage is to lower the rover with a tether and gently place it on the surface of Mars.
Removable walls and lid
All the wood panels (lid, sides, and ends) were a combination of a steel structure and 1/2" fire retardant plywood. The panels are attached together with bolts and T-nuts integrated into the steel tubing. The walls were secured with through bolts to a steel beam running the perimeter of the deck. By using bolts, as opposed to nails and screws, we afforded the customer the option of many re-assemblies without the drawbacks of stripping material from the panels, adding value and longevity to the purchase.
The unbelievable strength of using steel to reinforce each panel and mounting location at the base provided an extremely strong box. Additionally, the steal beam attachment point allowed for one wall to be freestanding which invariably happened at each disassembly and assembly which allowed the customer to pass critical safety concerns during the aerospace packaging process.
Each panel has lifting rings rated at 2,500 lbs (5,000 lbs per panel) and proof tested to 1,150 lbs. This allowed for ease of removal as the customer had a crane in their testing facility.
Factor of Safety
The base had to meet the factor of safety strength tests of just under 30,000 lbs. To achieve this goal Valley Box used a combination of 4x8 lumber and 4x4x.25-tube steel.
- The base featured 4 x 8 steel runners under the base that allowed for 7 1/2" forklift entry.
- The steel beams are perpendicular to the wood skids adding incredible strength to the overall base structure.
- The deck is made of 1-1/8" fire retardant ACX plywood for strength and grade as the surface of ACX plywood allowed for even paint distribution.
Fire Retardant
Anyone who knows the history of space travel knows that fire is the worst enemy of spacecraft. This box met customer fire retardant safety requirements. All wood used in the construction of the wood container was treated with fire retardant. Additionally, Valley Box painted all wood & steel attachments with fire retardant paint. The steel interface, which comes into contact with the customer part, was powder coated.
![]() |
"Mars 2020 Media Day " created by Nasa-JPL Copyright: Some Rights Reserved. Hosted on Flickr |
Confidential File Sharing
If a customer is unable to share models of their part due to proprietary information Valley Box can design packaging, support, and mounting structures based on limited information such as; envelope size, allowable contact points, surfaces, and mounting holes. As was the case with this aerospace packaging shipping crate. Valley Box was able to accommodate this customer's design requests with limited file sharing.
Air Transit
This wood container had to comply with MIL-STD-1791 for transport on a C-17 aircraft, as well as act as a material handling fixture in a clean room. These two requirements drove the need for decompression accommodations and removable custom casters:
- CASTERS: By attaching the casters to the base it can easily be rolled in and out of a clean room. However, freight companies shy away from shipping containers with wheels on the bottom, as it makes the load hard to secure, so these casters were designed to be removed and shipped in a separate shipping crate.
- DECOMPRESSION: Decompression accommodations of 8.3 psi within 0.5 seconds were calculated by the customer and Valley Box left the appropriate size hole in 2 sides of the container to allow the customer to install the cartridge decompression filter.
Access Doors
Because of the size of the box in the complexity of removing a wall, the customer requested a set of access doors so personnel could check on equipment, and run tests, and diagnostics without having to remove a panel with a crane and tools.
Proof testing
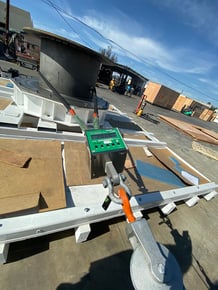
This container underwent rigorous factor of safety testing including;
- Walls: Dynamic hoist proof test of 2x load at 1,150 lbs
- Lid: Dynamic hoist proof test of 2x load at 1,900 lbs
- Casters: Dynamic proof test of 2x payload + top box at 15,307 lbs
- Base: Vertical Static Proof test of 28,197 lbs
- Base: Horizontal Static Proof test of 2,798 lbs
- Road Test: Dynamic proof test during transportation from Valley Box to customer location
Custom Instructions
Finally, a set of detailed assembly and disassembly instructions were made for the customer. This ensured that personnel unfamiliar with the box would be able to operate it in the safest most efficient way.