It takes a tremendous amount of coordination, strength and precision to move materials in just about every manufacturing environment. Many manufacturers have discovered that introducing industrial carts into their existing assembly lines can improve their bottom line by reducing worker injuries, increasing productivity, and allowing workers to focus on the highest-value production activities.
Between loading docks, storage areas, workplaces, and even within the most unyielding assembly lines —customized industrial carts can assist in the delivery of components and parts to assembly line workers line-side at the exact point of assembly.
The popularity of material handling solutions rests with the numerous benefits it provides manufacturing businesses:
- Improve work flow and shorten production times
- Eliminate parts collection downtime
- Free skilled employees for higher-value activities
- Clear factory floor space
- Free up capital
Ready to get your project started?
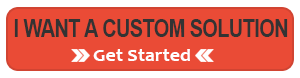
The following are 5 ways a custom industrial cart can support operational flexibility and safety best practices at manufacturing facilities:
#1 Safety
Avoiding employee injuries is paramount to any Safety Program. Lifting, twisting and bending in order to handle parts during assembly can lead to injury. By reducing or eliminating the opportunity for employees to lift, twist, or bend manufacturers can reduce work comp claims, improve employee morale, and improve productivity.
Manufacturers may also consider that manual fork trucks can be some of the most dangerous pieces of equipment in the assembly line. Designing a line around avoiding the use of these fork trucks can significantly reduce work place accidents.
Read: Improve Worker Safety with Positioning Equipment
#2 Ergonomics
Companies like Valley Custom Fabricators can custom build a custom industrial cart and fixtures to meet worker mobility requirements. Additionally, customization options can allow workers to better access the transported items without difficulty.
Components can be added that further improve worker ergonomics such as: rollers, conveyors, hydraulic lifts, and clamps. The result of introducing custom industrial carts can be a significant reduction in worker injuries.
Avoid Workplace Accidents with Ergonomic Safety Equipment read more.
#3 Space Savings
A custom industrial cart can provide both horizontal transportation and vertical storage at the same time. The added transport assistance reduces the need to invest in other transport equipment such as pallets and manual fork trucks.
Eliminating this stationary storage and fork truck can free up valuable shop floor space and free up operating capital.
#4 Versatility
Custom industrial cart solutions often solve more than one manufacturing challenge. Handling equipment often aides with multiple part requirements because adjustable elements can accommodate size, weight, and transport variations.
Often carts are built to assist in the transport of raw materials, kitted parts, as well as finished goods. Kit part delivery to the appropriate station allows the most skilled production employees to continue working on the assembly line, rather than spending time acquiring parts.
Read: Multi-Use Systems: A Win-Win Strategy for Manufacturers
#5 Travel Flexibility
Instead of installing permanent overhead or floor assembly lines, some manufacturers opt for custom carts to transport product through the assembly line—creating a continuous build line. Should production processes need to change it’s less of a capital investment to make adjustments to the material handling fixture than to a permanent installation.
Using this cart concept, it’s also very easy to pull a part off the line for quality inspection at any point during production.