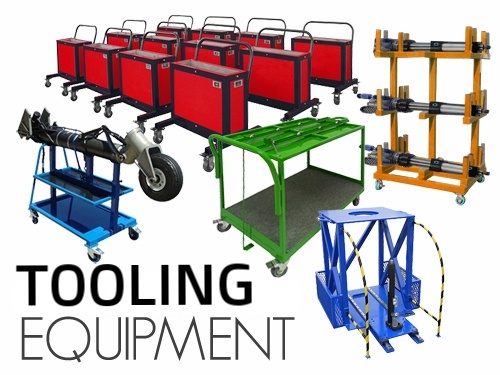
It’s official, reducing or eliminating waste has become the #1 priority in every major industry from aerospace to water. These industries and others have adopted a range of systems designed to fight waste. Many manufacturers are leading the pack by practicing lean manufacturing, which means they do more with less by employing lean thinking.
Find out how you can incorporate lean thinking into your processes!
Lean manufacturing was developed by Toyota executive Taiichi Ohno during post-Second World War reconstruction period in Japan, and popularized by James P. Womack and Daniel T. Jones in their 1996 book “Lean Thinking.” This way of doing business involves never ending efforts to eliminate activities that consume resources without adding value.
In order to implement lean manufacturing successfully, manufacturers should consider applying lean thinking to their material handling equipment. Industrial carts can help eliminate inefficiencies in an assembly line, which will:
- Optimize production
- Enhance worker safety
- and Maximize floor and storage space.
Slow production, worker accidents and a lack of space wastes precious time and money. When industrial carts are customized to the task at hand, the investment will pay for itself cost savings through efficiency, employee accident reduction and lower work comp rates. To find the right fit, start with the basics by considering lean material handling equipment that simplifies, creates flow and eliminates waste.
Bottleneck Analysis
A Bottleneck Analysis can help improve throughput by strengthening the weakest link in the manufacturing process. In technical terms, a bottleneck is a point of congestion in a production system that occurs when workloads arrive too quickly for the production process to handle. The inefficiencies brought about by the bottleneck often create delays and higher production costs.
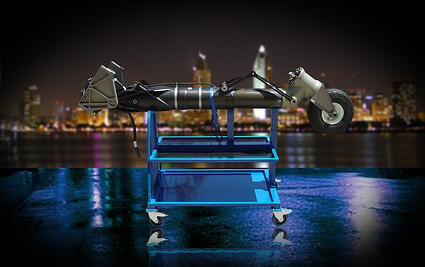
So think of a bottle and its shape. The fact that the bottle's neck is the narrowest point makes it the most likely place for congestion to occur, slowing down the flow of liquid from the bottle.
Applying the right solution can eliminate the bottleneck. Industrial carts are often a combination of products integrated into one system to prevent bottlenecks. A good example of this would be a custom industrial cart that is used as a build stand which can be utilized throughout the entire assembly line. This type of cart can eliminate time-consuming part transfer time.
Must read article: Multi-Use Systems Material Handling Equipment, a Win-Win Strategy for Manufacturers.
Continuous Flow
Continuous flow is manufacturing where work-in-process smoothly flows through production with minimal (or no) buffers between steps of the manufacturing process. Says Throughput Solutions, a Utah-based lean manufacturing training service;
“...once you begin producing a product you keep it moving through the value stream without placing it into a holding area for later processing. This helps avoid “batching” and increasing inventory levels.”
Customizing storage equipment to become mobile carts can:
- Enhance processes
- Increase safety
- Eliminate clutter
- Organize other equipment and tools
- Preserve precious floor and storage space
In the example to the right these storage bins had wheels and handles added in order for the manufacturer to expedite part acquisition.
Must read article: Why You Should Invest in Storage Equipment.